flooring

Car Park Coating System
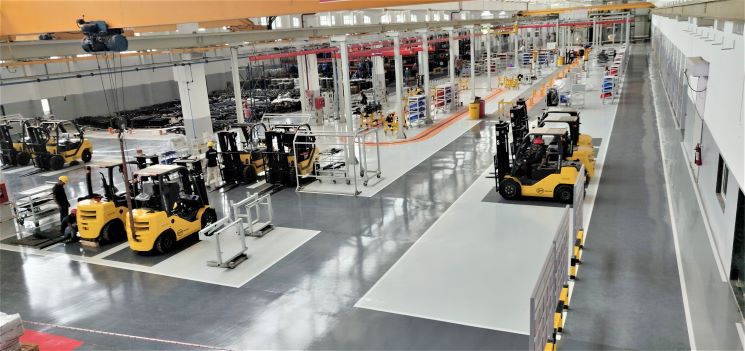
Epoxy flooring and Glass flake Epoxy floor coating
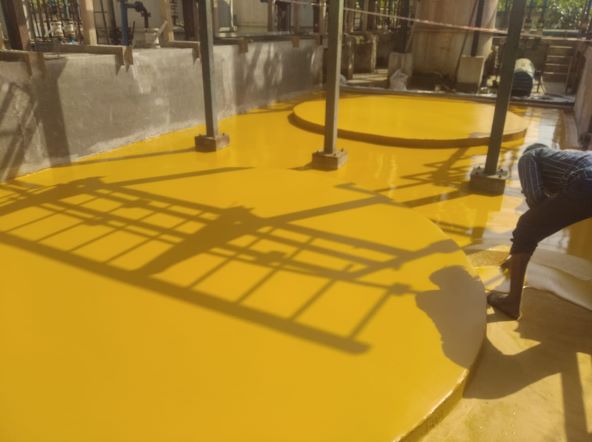
Polyurethane Flooring and Coatings
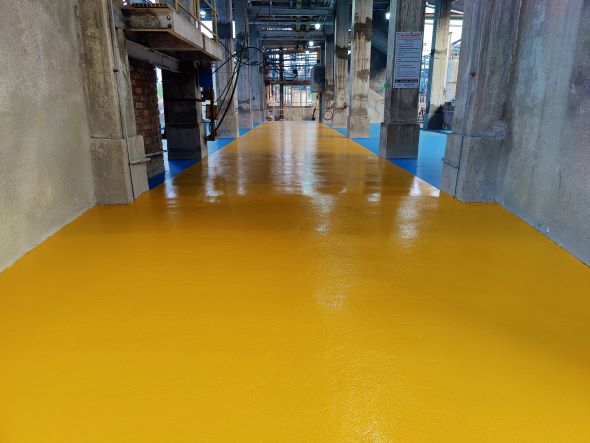
Polyurethane Concrete
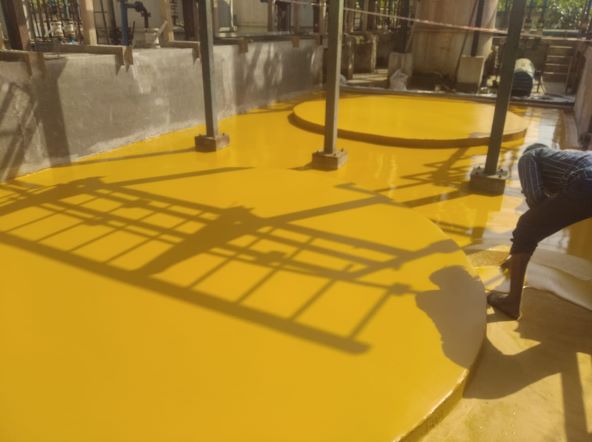
Anti-Static Flooring and Di-electric Flooring/HVI Coating
COMPLETE PROTECTION OF PARKING STRUCTURES
Car parks provide protection to thousands of cars every day. However, what about the parking structures themselves? If the structure and building envelopes are not protected, or inadequately protected, this can cause owners and operators many unpleasant and costly surprises. We provides high quality products and systems to provide complete protection with no nasty surprises
A combination of systems can be produced using the various products within the range to ensure that final protection and finish offered are tailor-made for the end use of the floor. Ramps, turning circles and parking bays require the extra protection this flexible system offers. What’s more, the final PU Topcoat can be produced in a wide range of attractive colors to match the surrounding décor. This full system represents the latest in reinforced glass flake epoxy and polyurethane technology, and completely outdates the use of aggregate/sand as a reinforcement to the coating.
Advantages of Car Park Coating System
- Optimum economical protection
- Glass flake gives ultimate protection of high wear areas
- Outstanding long-term resistance to abrasion
- Low maintenance cost and easy to maintain
- Chemical and UV resistance
- Flexibility
- Wide range of attractive colors
- Aesthetic
- It reduces structural load, which increases due to traditional parking systems like Parking tiles and IPS Flooring.
- PU car park coating system thickness is less, compare to traditional parking systems, so client can get benefit of maximum parking height.
- Seamless coating and water impermeable property which protects structure from water penetration and concrete deterioration.
Epoxy Flooring
Seamless, self-smoothing architectural flooring system based on an advanced solvent free epoxy resin system and selected graded aggregate. The smooth impervious surface finish provides an easily cleaned and hygienic surface with excellent resistance to chemical and mechanical attack.
Application areas:
- Pharmaceutical and cosmetic industries
- Laboratory areas
- Medical facilities
- Clean rooms and other sterile areas
- Showrooms
- De-contaminable areas
- T.V. studios
- Warehouses and high rack storage
- Laundries
Systems :
– Self leveling Epoxy flooring – 1mm to 4 mm
– Epoxy Screed – 1 mm to 12 mm
– Epoxy Coving.
Glass Flake Epoxy Coating
Scope:
This is a two component amine cured, glass flake reinforced, abrasion resistant epoxy coating. It is a high solids, high build product. It is a high performance product. It is specially designed as an abrasive and impact resistant coating for areas with extreme wear and tear. If enhanced slip resistance is required Jotafloor Non Slip can be used in the system. Can be used as mid coat or finish coat in atmospheric environments. Specially suited for properly prepared concrete substrates.
Application areas:
Suitable for a wide range of floors with various levels of mechanical and chemical exposure. Specially designed as a part of a complete system for heavy duty traffic, such as ramps, car parks, parking bays, pedestrian walkways and industrial floors. Recommended for car parks, warehouses, garages, dairies, factories, laboratories, aircraft hangars, food, beverage and plant rooms.
Seamless, self-smoothing heavy duty Polyurethane based flooring system
How does Polyurethane flooring work?
It is a multi-component, Polyurethane based system for the protection of concrete floors subject to high levels of traffic, impact and abrasion. Its enhanced flexibility provides excellent impact resistance and reduces the risk of cracking due to substrate movement. Polyurethane is available in smooth or slip-resistant profile.
Polyurethane flooring recommended for?
Due to its excellent impact resistance, Polyurethane is recommended for industrial floors, which require a matt, durable abrasion-resistant finish such as loading bay areas, production/assembly halls, exhibition halls, hospitals and schools, warehouses, service corridors, aircraft hangars…
What are the advantages of PU
- New generation of PU topcoat with high performance .
- Semi-gloss finish.
- VOC and solvent free.
- Very low emission
- High Abrasion resistant.
- Improves scratch and wear resistance.
- UV stable and Easy to clean: low maintenance costs.
- High durability.
- Aesthetically pleasing
- High hiding power even at low consumption and therefore economic in use
Polyurethane Concrete
- New product systems, all based on the original, unique polyurethane concrete, concept, have been introduced to offer end user clients a wide range of additional properties including: defined slip resistance, anti-static/ static dissipation, aesthetic appeal, and fast return to service.
It is cost effectivebecause it is long lasting, quick and practical to install and meets all the needs of modern processing industries.
Advantages:
- Fast application and curing: Even at low temperatures. Specifications are available that are fully serviceable after only 5 hours at 10°C, making it ideally suited for refurbishment work.
- Durable: Excellent impact and wear resistance. Many 10–20 years old floors in aggressive environments are still in service.
- Slip resistant flooring: Different grading for specific demands.
- Hygienic: HACCP certified, it is hygienic as it can be cleaned to same level as stainless steel. Certified with the Eurofins Indoor Air Comfort Gold standard for low emissions, it’s non-tainting and not smelling, meaning no delays in restarting operations.
- Temperature resistant: Withstands spillages up to 120°C depending upon specification as well as freezer temperatures to -40°C.
- Non-tainting : Even during application in food handling areas.
- Moisture tolerant: Can be installed onto 7-day old concrete without the need for special primers, helping to maintain program on fast track projects.
- Chemical resistant: From strong acids to alkalis, fats, oils and solvents which can rapidly degrade other types of resin flooring.
- Antistatic: Conductive properties to control undesired static electricity.
- Sustainable: Durable materials and low VOC emissions.
Anti-Static Flooring and Di-electric Flooring/HVI Coating
Anti-Static Epoxy flooring
- Scope: Conductive/ Dissipative system have been designed for use in areas where a static Conductive or a static Dissipative floor is required as a measure to control static electricity. Moreover, they provide a dense, impervious, colored and chemical resistant floor surface which is hygienic and easy to clean. Typical areas of use include electronics manufacture and assembly, clean rooms, computer rooms, hazardous dust and chemical environments and hospital operating theatres.
- Advantages:
- Static control : provides an effective passage of static electricity to earth.
- Hygienic: provides a dense, impervious seamless floor surface which is easily cleaned.
- Durable: good abrasion resistance.
- Aesthetical appearance: available in a wide range of colors to enhance the working environment.
- Chemical resistant: good resistance to a wide range of chemicals
Di-electric Flooring: Pro Epishield HVI Coating:
- Scope: Seamless, Self Leveling, High Voltage Insulation coating, based on epoxy resin reinforced with special type of fine aggregates and is available in assorted shades for application on concrete floors. Possess excellent break-down voltage resistance as required for high dielectric strength protection on concrete substrates.
- Uses: Recommended for protection of concrete floors for wear and tear, easy cleaning, protection of concrete to corrosion, while it gives the primary advantage of safety against injuries caused by electrical leakage & tracking by providing the required insulation to Ultra High Voltage. Used in panel rooms, HV Control rooms to provide a dust free, clean and durable floor coating.